A BFM® fitting comprises a unique snap-in BLUEBAND™ flexible connector that sits between two specially formed steel spigots welded to an inlet and outlet in a process line.
Together, the system eliminates the problems associated with old-fashioned clamp-style flexible connectors.
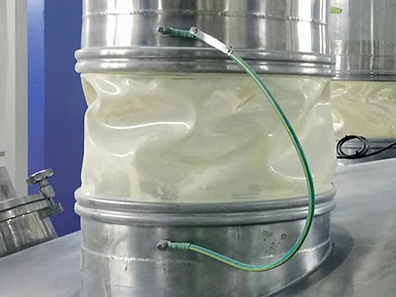
BEFORE & AFTER
The BFM® Difference
Use the slider to see the difference!
WITH TRADITIONAL METHODS
- Powder leaks through clamps
- Difficult to fit, variations & inaccuracies
- Overpressure causes high-risk clamp failure
- Frequent downtime for replacements, clean-ups
THE BFM DIFFERENCE ENSURES
- No dust leakage and better hygiene control
- Easy snap-in system and helps to streamline inventory
- Stronger pressure resistance and reduced explosion risk
- More durable material, quick change overs and less downtime.
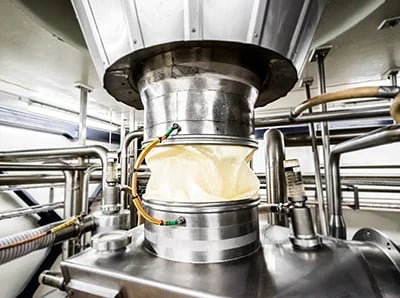
The BFM Advantage
BFM® Keeps Products Flowing
Improved hygiene
Cleaner
Our BFM® flexible connectors are cleaner due to their unique blue band, a snap-fit design that closes from the inside.
This enables a 100% sealed system that:
- Prevents product leakage
- Stops product build up, lowering contamination risk
- Eliminates dust
- Eases flushing
Peace of mind
Safer
Bulk processing plants have many situations and equipment where staff health and safety can be compromised.
Flexible connections between machinery can be a location for safety issues with potential dust leakage and the possibility of combustible dust explosions being a major concern.
The BFM® fitting flexible blue band connector system provides peace of mind that safety is being improved for your staff.
THE BOTTOM LINE
More Efficient
When your flexible connectors tear or leak constantly, the efficiency of your production line reduces dramatically.
There's downtime needed to replace the connector and labour costs in cleaning up product spillage. And then, of course, there is the cost of wasted product itself.
To improve your operational efficiency, you need to have durable, quality flexible connectors that last the distance and perform consistently, so your production can continue without interruption.
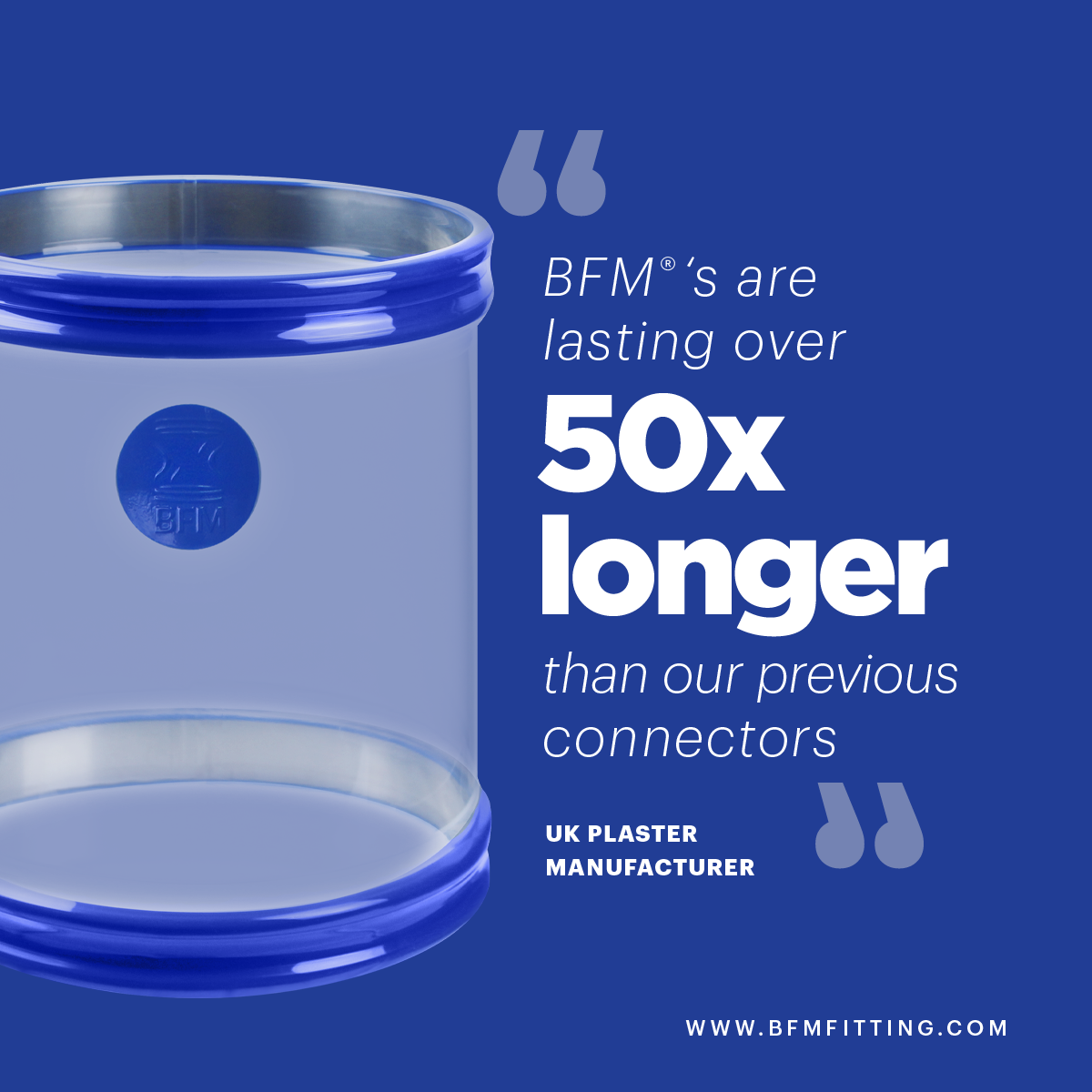
BFM fittings System
A BFM® fitting comprises a unique snap-in, blue-banded flexible connector that sits between two specially formed steel spigots welded to an inlet and outlet in a process line.
Together, the system eliminates the problems associated with old-fashioned clamp-style flexible connectors.
HOW WE WORK
Upgrade Your Skills Upgrade Your Life
Spend some time to visit our website or head office and discover our current courses, enrollment procedure, and registration deadline. We are opening new classes every beginning of each month.
The BFM® fitting system outperforms other flexible connectors in virtually every application, making them the connector of choice for the world's leading food, chemical, pharma and mineral processors. Here's why:
Quick Changeovers
The snap-fit designs mean BFM® fitting connectors have the fastest changeover in the market - most can easily be replaced in less than 30 seconds.
Improved Hygiene
There's no product build-up and easy flush through for cleaning provides a much more hygienic connection solution than clamped products where crevices can breed bacteria.
Reduced Downtime
Faster changeovers, longer-lasting materials and less dust leakage mean there is significantly less lost production time for connector replacements and clean-ups with BFM® fittings.
Better Health & Safety
No tools required for installing standard BFM® connectors, plus less dust escaping into the plant combine to make a healthier and safer environment for staff.
No Product Loss
The 100% seal and the durable nature of the connectors mean no valuable product escapes during normal production and no spillage due to connectors tearing.
Explosion Resistant
The snap-fit internally seated cuff and spigot design seals tighter under pressure and the Seeflex range of connectors have been explosion tested in excess of 60kPa.
Regulatory Compliant
BFM® fitting products have been independently tested and conform with the leading internationally recognised health and safety legislation.
More Durable
The materials and design of the BFM® fitting connector system are extremely long-wearing and durable so they don't need to be replaced as often as other connectors.
Streamlines Inventory
The BFM® fitting system simplifies and streamlines inventory control, improves supply chain sustainability and the standardized, exact sizes ensure a perfect fit every time.
BROCHURE DOWNLOAD
BFM® fitting
The new industry standard for flexible connectors
Every processing industry needs flexible connectors. BFM® will keep your factory cleaner, safer and more efficient.
BFM®'s patented blue band connectors are trusted by many of the world’s largest chemical, food, mineral and pharmaceutical companies to keep their facilities dust-free, improve health and safety, and reduce production downtime.
It's a revolution in connector technology that has set a new standard in quality and performance.
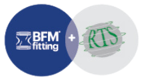
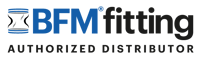

Downtime Significantly Reduced for 24-Hour Flour Miller
“They’re one of the best things we’ve found…since installing the first two fittings, we’ve been replacing all of the remaining clamp-and-sleeve connectors in the facility with BFM® fittings. I’ve been putting them everywhere there’s a transfer point because they make things so much easier for our operators.”
Superintendant of Engineering and Maintenance
Case Study provided courtesy of BFM® Distributor Powder-Solutions Group (United States)
CLEANING & REFITTING PROCESS SIMPLIFIED

Change From Clamped Connectors Helps Retain Valuable Product
"BFM® fittings were installed to replace all existing hose-clip type connections on both the ultrasonic vibrating sifter and electronic magnet filter.
Now the internal cleaning process can be completed in a much shorter time due to the fast and easy snap-fit removal and re-installation process of the BFM® fitting."
Factory Manager
Case Study courtesy of BFM® Distributor International Chemical Scientific (South Korea)
BFM® FITTING CONTAINS SUPER-FINE POWDER

Increased Production Efficiency
“Shortly after buying the first two BFM® fittings over 13 years ago, our Continuous Improvement LEAN Process outcomes demanded we purchase more due to the time savings during set-ups, the reliability of a good seal and the ease of assembly and cleaning for our operators. We have never had a BFM® connector let go or lose product which would be a costly event in the pharma industry. We now have them fitted to all our gravity transfer systems and product mixing bins.”
Engineering Supervisor,
Global Nutraceuticals Manufacturer, (Australia).
EFFICIENCY GAINS FOR NUTRACEUTICAL PROCESSOR

Connectors Now Lasting Over 50 Times Longer
“Plaster is very fine and gets everywhere. It is difficult to contain, particularly when your connecting sleeve has holes in it! BFM® has been brilliant. The connector seals inside the spigot so it can’t chafe on the sharp edges and there are no jubilee clips to tear the fabric. It lasts for longer and best of all it doesn’t leak any dust.”
Works Engineer
UK Plaster Manufacturer
Case study courtesy of BFM® Distributor ProSpare (UK)
PROBLEM POWDER CONTAINED ON SIEVE