WYE LINE DIVERTER
Worldwide, plant managers and maintenance engineers recognize the Vortex® Wye Line Diverter™ as the industry standard dilute phase diverter specifically designed for handling dry bulk solid materials.
Ideal application: Diverting or converging materials in high cycle applications. Common in storage fill and/or storage transfer applications. When applied in minimally abrasive applications or as an air directional valve, Wye Line Diverters often record more than 10 million cycles over the course of their service life.
Vortex keeps you up and running.
In your world there is no time for downtime.
That's why Vortex makes solids and bulk handling components that are made to perform.
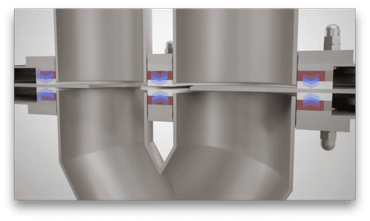
Live Loaded, wear compensating hard polymer pressure plate seals
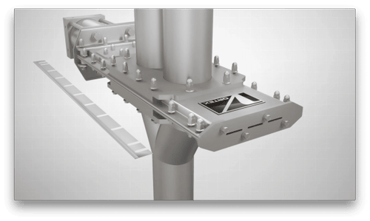
Shimming system for
in-line maintenance

Machined, full-bore orifice for unobstructed material flow and to maintain convey line pressures
Key Features
-
Live Loaded, wear compensating hard polymer pressure plate seals
-
Shimming system allows for in-line maintenance
-
Machined, full-bore orifice for unobstructed material flow & to maintain convey line pressures
-
Can be shifted on a flowing column of materials
-
Positive seal of materials & dusts across the closed port(s) and to atmosphere
-
Mechanically self-cleans its seals with each actuation
-
No pinch points or exposed moving point for safety
-
No internal cavities to prevent wedging, lodging & spoilage
-
Narrow profile for limited space applications
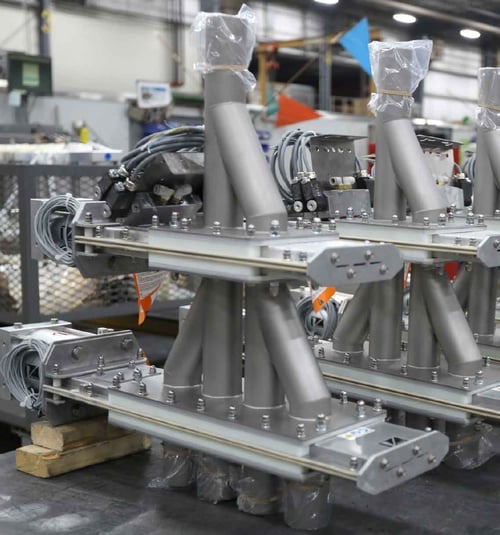
Options
.jpeg)
Vortex Wye-Line Diverter versus Alternatives
Power of Comparison
- Many alternative pneumatic diverters rely on soft rubber seals which are directly exposed to the material flow stream. These seals rapidly erode or tear away in service, as a result of blast abrasion. Such deficiencies promote leakage of air, materials and dusts through the valve and to atmosphere, in addition to actuation issues and several other maintenance concerns. The Vortex® Wye Line Diverter™ eliminates these issues by using "live loaded" hard polymer pressure plate seals. Hard polymer provides greater wear resistance and longer service life than alternative sealing materials. The hard polymer seals are "live loaded" with compressed rubber backing to ensure even as the polymer experiences frictional wear from many actuations over time, the rubber load seals continuously force the polymer seals against the blade. The seals are also shielded from the material flow stream, to protect them from blast abrasion. This design maintains the diverter's positive seal without frequent maintenance intervention.
- Plug diverters are prone to seizing and binding, as a result of material build-up in the clearances between the rotating plug and the diverter’s housing. The Vortex Wye Line Diverter’s sliding blade design mechanically self-cleans materials away from the sealing surfaces with each actuation. This prevents material build-up, reduces seal wear and ensures positive valve closure.
- Plug diverters are constructed primarily from bulky, heavy cast iron, making them costly to install or remove for maintenance. The Vortex Wye Line Diverter is lightweight and narrow profile, making it well-suited for difficult installations.
- In order to shift ports when using a plug diverter, the internal plug must be rotated approximately 150 °. This is often a timely process. Before the internal plug is rotated, the system’s blower must be temporarily deactivated. Otherwise, the plug will create back pressure as it rotates. With an average actuation time of 2 – 6 seconds, the Vortex Wye Line Diverter can be shifted without shutting down the system's blower and without creating back pressure.
- Many alternative pneumatic diverters have blade(s) and seals which are directly exposed to the material flow steam, creating wear. The exposed blade(s) and seals also disrupt convey line pressures and material flow as they pass through the valve, which can cause bridging, line plugs and other maintenance concerns. To resolve these issues, the Vortex Wye Line Diverter’s sliding blade is machined with an unobstructed, full-bore orifice that maintains convey line pressure and allows unrestricted material movement.
- The Vortex Wye Line Diverter creates a naturally occurring high-pressure airfoil that deflects errant materials away from the closed port(s) and back into the material flow stream. Also, with each purge cycle, the Wye Line Diverter forces residual materials downstream. This design prevents material cross-contamination to the opposite port(s).
- Alternative pneumatic diverters can significantly shear materials, as a result of jamming and grinding materials into the seals. Sheared materials cause seal wear, material degradation and damaged product quality. Sheared materials may also wedge in the seals, causing the diverter to seize and bind. To prevent these issues, the Vortex Wye Line Diverter's "scissoring" action tapers off material flow as it shifts between ports. In doing so, the service life of the pressure plate seals is also extended.
Wye Line Diverter Handling Polymer Pellets
The challenge was to provide a diverter capable of withstanding the abrasiveness of fiberglass-filled pellets.
This US-based division of an international company manufactures an extremely abrasive grade of polymer pellet. As such, the company’s UK-based sister facility advised that they source new material transfer components capable of withstanding the product’s abrasive characteristics.
Wye Line Diverters Handling Semolina Flour
When the Quality Control department of this pasta plant began to notice small pieces of metal appearing in their semolina flour, a quick investigation immediately found the cause. As different component parts within the conveying system were removed for inspection, it was found that metal shavings were making their way into the cast housing of five diverter valves.
How to Select a Valve for Solids & Bulk Handling
Many people think that selecting a slide gate or diverter for handling dry material should be a relatively simple process. But in reality, valve suppliers need more information to accurately select the right valve for the application.
So, let’s begin with the premise that each application for a slide gate or diverter valve has its own unique requirements. What are the factors that determine what type of valve is selected and what modifications are necessary?
Vortex Multi-Port and Wye Line Diverters assist with donut production
Vortex Multi-Port and Wye Line Diverters assist with donut production by pneumatically conveying various grades of flour from two sources toward any of eight destinations, for packing.
The Challenge: Rather than a hose manifold station, automate the process of switching convey paths for materials traveling toward several packing stations
Latest Blog Posts
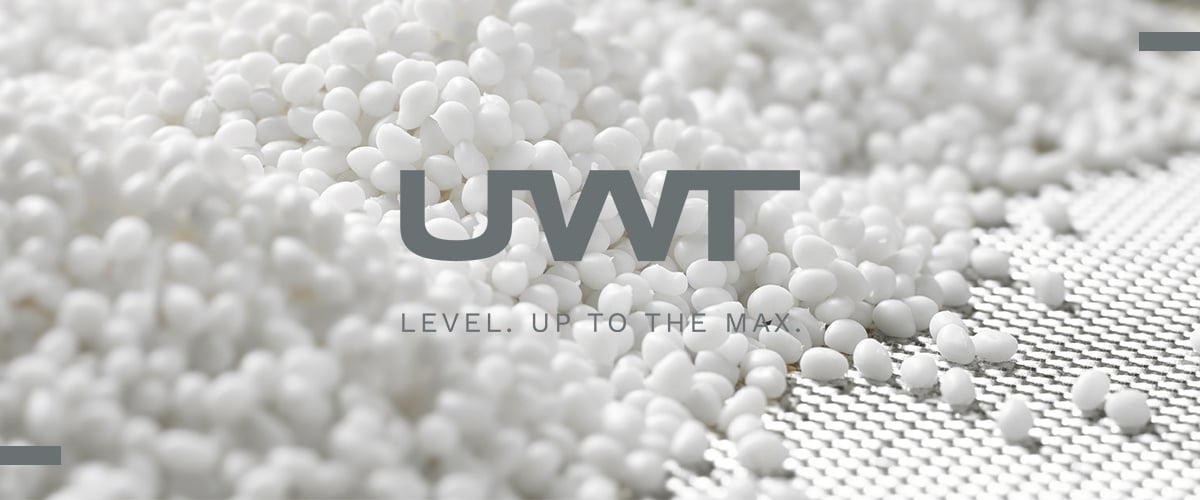
Efficient Level Control in EPS Industry
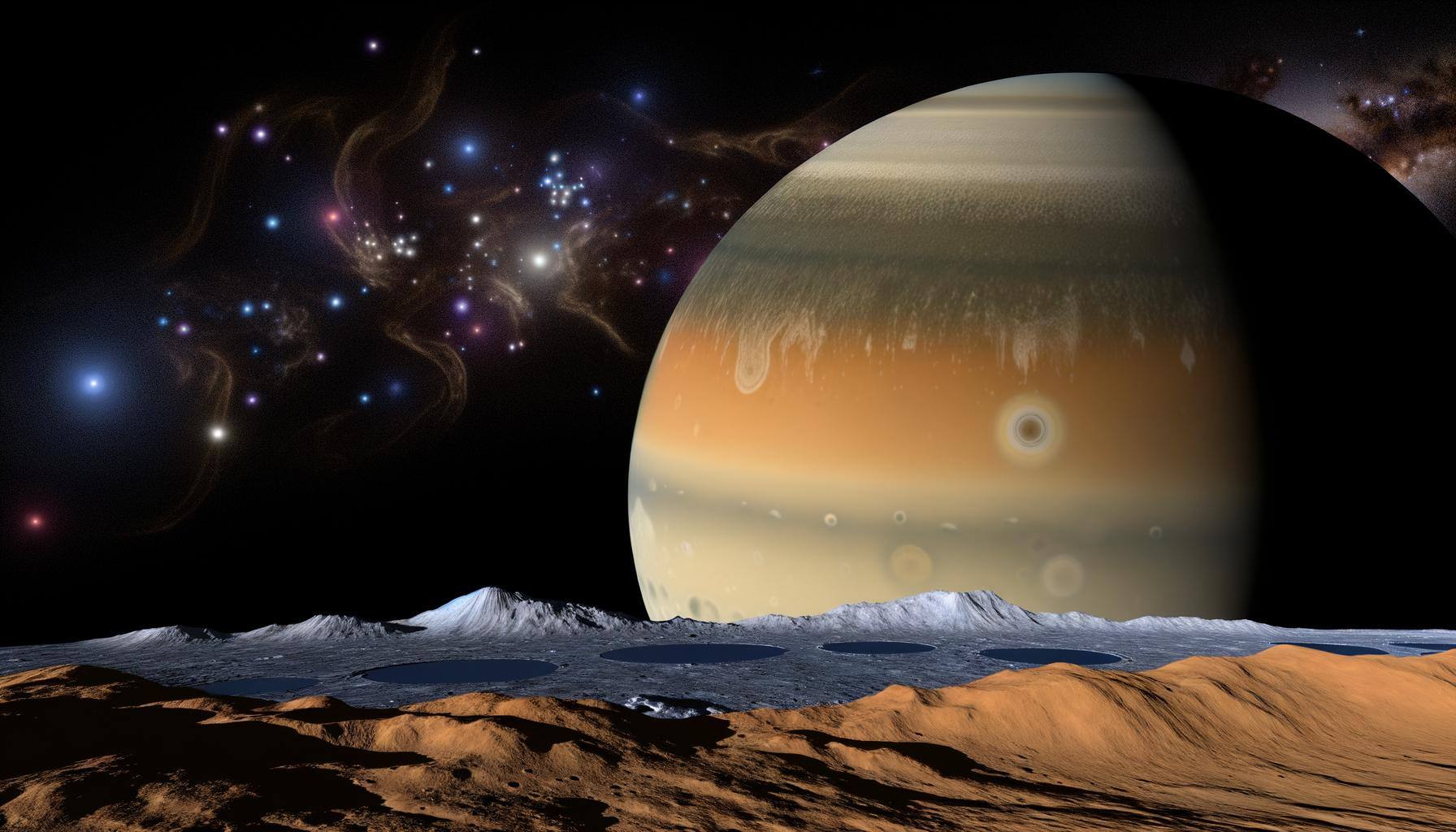
Design Solutions for Abrasive Applications
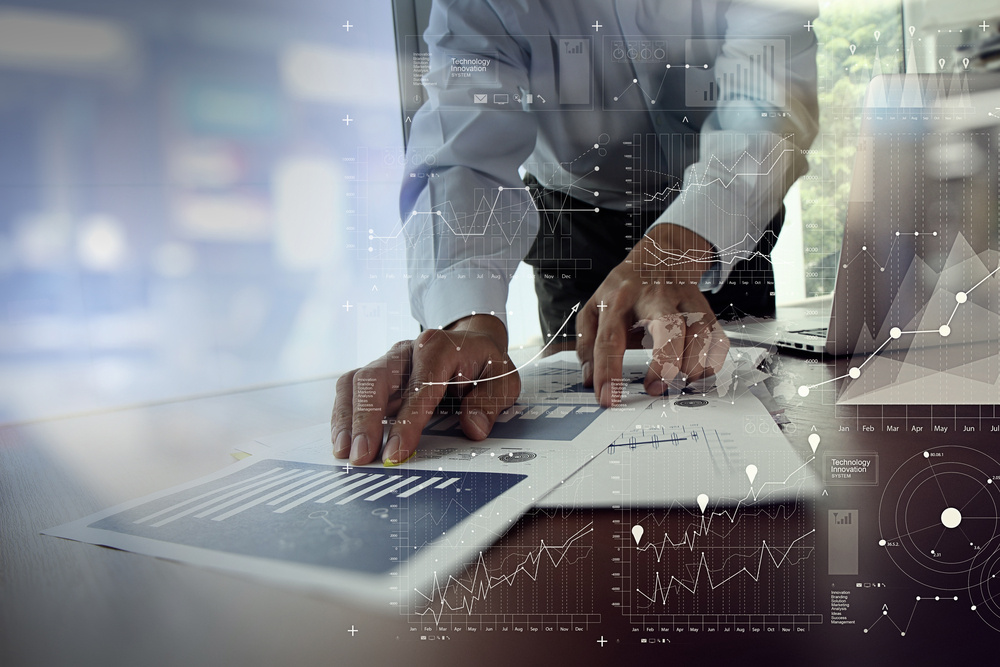
Efficient silo management for smooth process flow
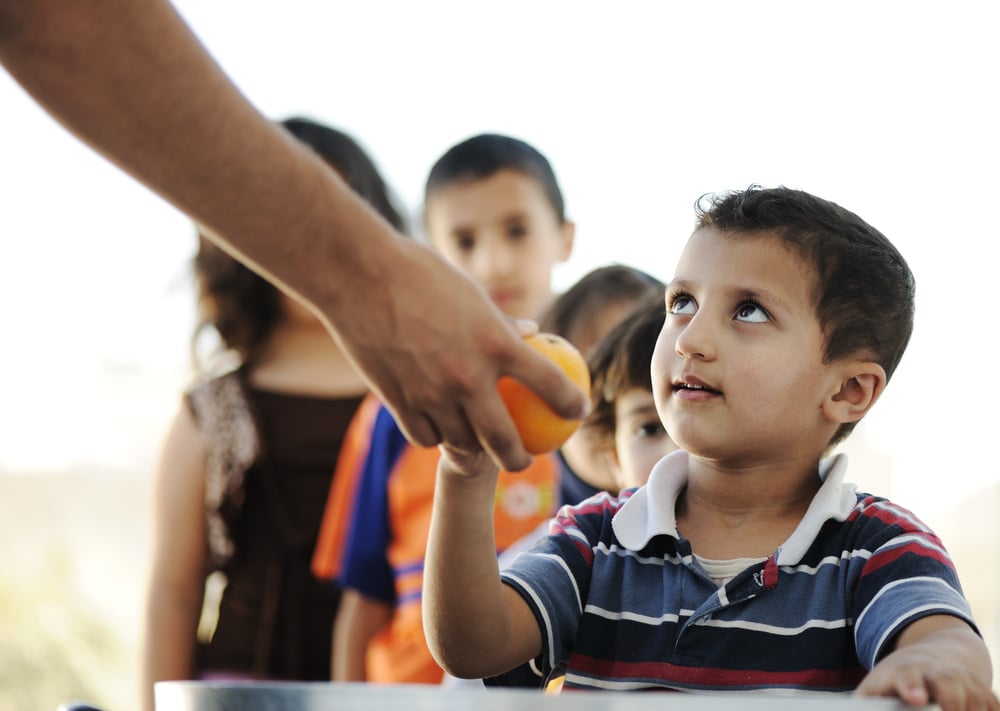