This informative article by David Boger, Vice President - Global Business Development and Marketing, Flexicon Corporation - will help you to accurately select an appropriate bulk bag filler for your manufacturing process.
Please read the article excerpted below or read the full article here.
Exponential growth in the use of bulk bags has spawned an entire manufacturing segment dedicated to producing specialized equipment that not only fills and discharges bulk bags, but offers various degrees of automation and integrates filling and unloading operations with upstream and downstream equipment.
As the number of equipment options increases, so should the ability of the specifier to evaluate stand-alone equipment and integrated systems against current and anticipated needs. The author addresses the "filler" half of the bulk bag handling equation, offering the six most important parameters to consider when satisfying any individual bulk bag filling requirement with top efficiency and cost effectiveness.
- Anticipate maximum capacity
The difficult but critical question: How many bulk bags will you need to fill per week during the useful life of your next bulk bag filler.
With few exceptions, buying a more costly filler with higher capacity than you now need will be less costly than replacing a filter you outgrow, unless that filler can be retrofitted with performance enhancements at a later date. Capacity requirements run the gamut from one bag per week to 20 bags per hour. Where your volume falls, should, in part, influence your decision to specify a manual, semi-automated or fully automated machine.
- Evaluate safety against manual operations required at any given level of capacity
With manual and semi-automated filling operations, the potential for worker fatigue and injury can increase according to required output per shift, relative to the type of bulk bag equipment specified.
Consider that the connection points of a conventional filler are often beyond the reach of most operators, even when short bags are being filled. But adding the height of a roller conveyor to the height of a bulk bag to the length of its bag loops puts the connection points for bulk bags of only 48 inches (122 cm) in height at approximately 7 feet (213 cm) above the floor!
- Ensure dust is contained
Even the most rudimentary filler is likely to be equipped with an inflatable spout seal (FIG. 7) to hold the bag spout firmly in place during filling. However, not every fill head is vented to a dust collector to filter displaced air and dust, and to vacuum ambient dust in the operator's vicinity during disconnection and cinching
- Determine your need for multi-function filling
If your plant fills drums, boxes or other containers as well as bulk bags, multi-function fillers (FIG. 8) can boost production, undercut the cost of separate equipment and reduce the amount of floor space required.
- Match the feed source to your material and your filler
Filling capacity, accuracy and efficiency are often limited by the ability of upstream equipment to feed material consistently and in sufficient volumes. High capacity, semi- or fully-automated fillers therefore require high-capacity feeding systems that are typically automated and feed material into the filler by gravity or by a metering device.
- Comply with sanitary requirements
While all fillers can be constructed of stainless steel with ground and polished welds, their designs can preclude sanitizing according to government standards.

Have questions about bulk bag systems?
We're always happy to chat.
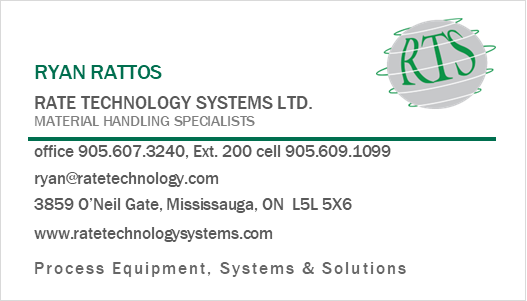
Don't have time to read the entire article? Prefer to listen? Hit the recording below to have this blog read to you.
Leave a Comment