In spring 2018, Vortex and Rate Technology Systems, a Canadian Vortex equipment sales representative, consulted with a horse feed producer to assist with a process need.
Application
At this facility, the client is producing forage cubes. Upstream in the process, bales of hay are broken down and minor ingredients are added before the raw materials are formed into cubes (approximate size: 3 – 4 in | 75 – 100 mm square). Once formed, the cubes are transferred into cloth silos. Below each silo, a common belt conveyor transports forage cubes to a packaging line, where they are loaded either into 50 lb bags or into bulk bags.
Vortex and Rate Technology, Inc. were tasked with identifying a solution for discharging forage cubes out of the cloth silos, down onto the belt conveyor. Primarily, the client is concerned with forage cube quality and thus, the cubes cannot be damaged upon gate closure.
Solution
Upon careful analysis of the application, the Vortex Roller Gate was recommended.
The client’s specifications include:
- Quantity: 2
- Gate Size: 36 in | 915 mm
- Gate body constructed from 6061-T6 aluminum.
- Blade & seal retainers constructed from 304 stainless steel.
- Material contact areas constructed from 304 stainless steel & polymer.
- Each equipped with a Special Service Inlet.
The client sourced this small-batch order as part of the “proofing” stage of its new production process.
Features
The Vortex Roller Gate offers many key benefits, including:
Wear-Compensating

Bonnet seals constructed from hard polymer and “live-loaded” with compressed rubber backing. This ensures that as the polymer experiences frictional wear from many cycles over time, the rubber load seals continuously force the seal plates against the sliding blade. In doing so, the gate is able to self-maintain its dust-tight seal without frequent maintenance intervention.
Performance

On each opening stroke, the Roller Gate’s bonnet seals act as squeegees, forcing any materials remaining on the blade to fall away into the process line below, rather than migrating into the bonnet area. This prevents actuation issues associated with material build-up in the bonnet area.

By design, a Special Service Inlet acts as a funnel to direct material flow through the center of the gate. The primary purpose of a Special Service Inlet is to create a void between materials, the blade, and the gate’s seals. In this application, a Special Service Inlet prevents the blade from chopping the forage cubes and packing materials into the end seal.
In-Line Maintenance
Along the lateral aspects of the gate are two bonnet seal access doors. Both doors are removable using only simple tools. Once the doors are removed, new upper and lower bonnet seals can be driven into the port while the worn seals are simultaneously ejected out the other side.

After many actuations over time, frictional wear between the Roller Gate’s sliding blade and the gate’s hard polymer side seals may also lessen its sealing effectiveness across the blade. Rather than removing the gate from service to replace its side seals each time, the Roller Gate features CAM-adjustable rollers. Using only simple tools, the rollers can be rotated upward to “lift” the blade back into position and restore the compression between the blade and side seals.
Prolonged Service Life
The Vortex Roller Gate is designed with several replaceable parts, including blade, clevis, internal seals and retainers, actuator, position indication switches, and more. If a slide gate is maintained and operated as recommended, these mechanisms should be the only wear parts. In many cases, this maintenance-friendly design has allowed Vortex slide gates to remain in service for many years – and sometimes, even decades.
Employee Safety

The Vortex Roller Gate prevents material leakage and is dust-tight to atmosphere. This allows for good housekeeping, and benefits occupational initiatives by ensuring a safe and healthy work environment. The gate is also designed with no pinch points or exposed moving parts, for operator safety.
Update: In-the-Field
Now installed in their application, the Vortex Roller Gates have exceeded the client’s expectations for quality and performance. More specifically, the client is pleased that the Vortex Roller Gates do not damage the forage cubes upon gate closure. In fact, the client has since specified the Vortex Roller Gate as its standard for this application. By year-end 2019, the facility will have Vortex Roller Gates on each of their 79 production lines.
If you'd like to learn more about Vortex Roller Doors, give us a shout or book a meeting.
We're always happy to chat!
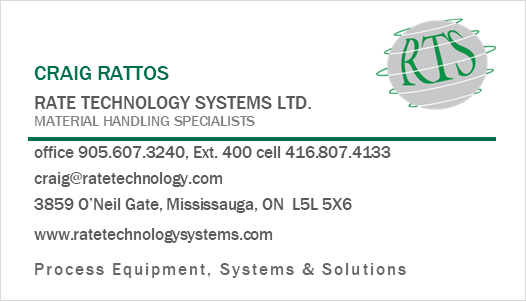
Leave a Comment