DAIRY PROCESS
Rotary Valves
Dairy Plants achieve sanitary processes with Rotary Valves
Dairy plants commonly use Rotary valves in their process in order to meter product flow through a system, as well as lock out any system air from further downstream process. The dairy sector relies on hygienic and cleanability features . We have a clean in place design as well as a 3A compliant GHA Rotary valve.
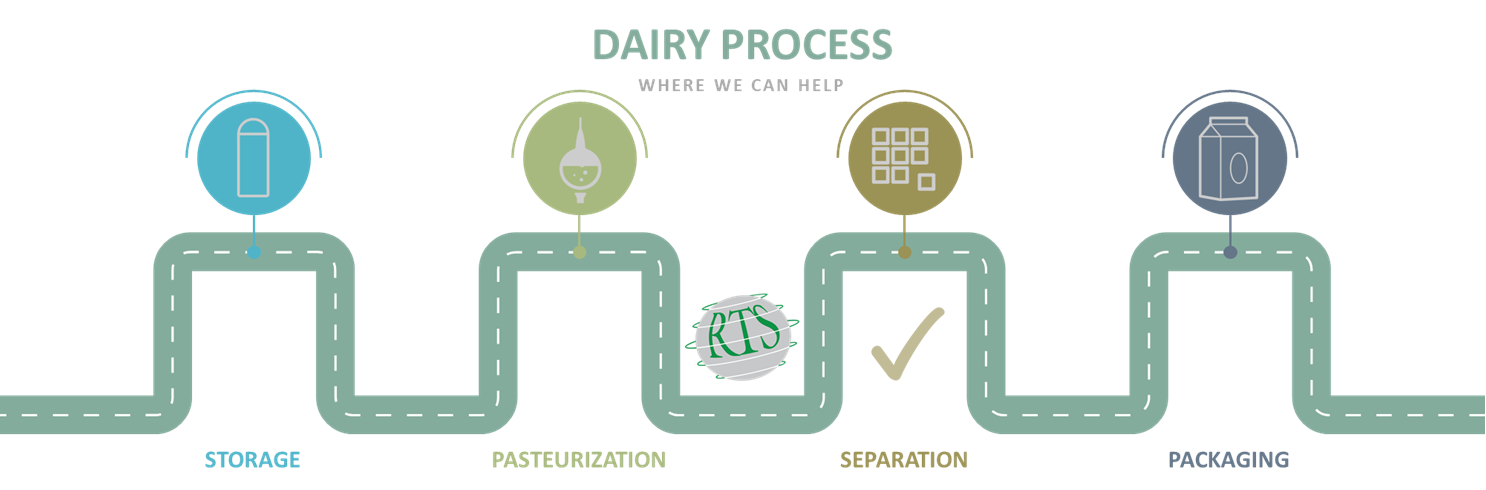
Rotary valves are used to control flow of a material in a process, as well as to lock out air.
Global cleanable airlock (GCA) - Airlock for sanitary processes
Two models of the GCA consist of a standard and a demountable unit. The standard model is a round inlet, round outlet rotary valve which incorporates seals and product contact surfaces which meet food safety requirements. The demountable unit is designed with a rail system that simplifies removal of the endplate/rotor assembly from the housing providing access to the internal valve cavity, rotor pockets and all other product contact areas for quick and easy cleaning.
Other key features of the GCA Airlock include:
- Easy access to seals with rotor removed from endplate
- All stainless steel construction with the exception of the endplate bearings
- Housing and endplates designed for 10 Bar explosion shock resistance
- FDA and EC 1935/2004 approved materials of construction in product contact areas
- Oversized rotor shaft creates a naturally radiused rotor pocket for more complete product release
Reliability, strength and quality
Our collection of valves are highly efficient, rugged and reliable and are suitable for vacuum dense phase, dilute phase, and gravity discharge systems. They are precision-crafted at extremely close tolerances to:
- Eliminate dusting
- Reduce maintenance costs
- Avoid process shutdowns
Valve performance depends directly on the material being handled. We’ll help you properly size the correct valve for your applications, and select appropriate housing and rotor options to manage your desired rate and the estimated fill efficiency. Our state-of-the-art pneumatic TestCenter can test your material and prove systems before any steel is cut or equipment is installed. You can count on us to properly size valves and blowers to reduce air leaks, decrease energy costs, and ensure proper convey pressures and rates — guaranteed.