Dairy Process - Fittings
Dairy Plants are required to be of the highest sanitary standards
Dairy plants are required to be of the highest sanitary standards, with a need for continual cleaning, such as CIP (Clean in Place). They are also environments that need to be free from dust, with the risk of dust explosions.
The BFM® fitting is the perfect solution. As well as offering a component that is more abrasion-resistant than traditional connectors, the BFM® connector is easily replaced (less downtime), easily cleaned, and 100% dust-tight (eliminating plant contamination).
BFM® fittings "fit" into every stage of the dairy process from storage to packaging. Ask us how they can help you achieve the highest possible hygiene in your dairy environment.
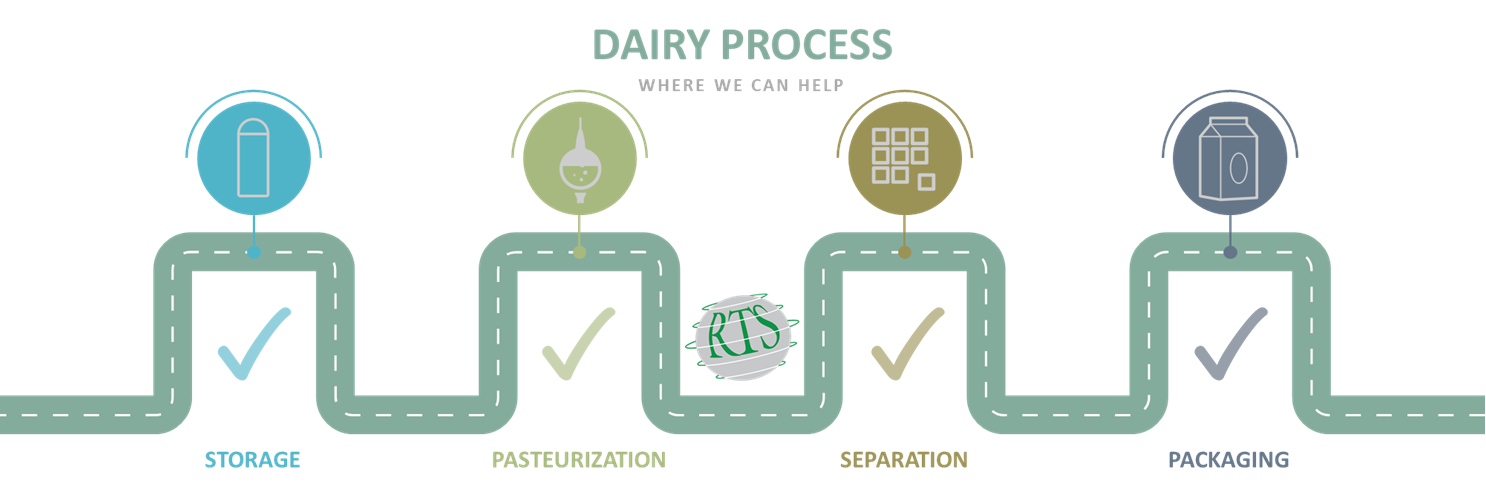
A good fittings system will keep your production areas cleaner, saving you valuable time, money and provide a better environment for staff.
Some of the benefits of BFM® Fitting system:
![]() |
Improved hygiene: There is no more dust leakage, eliminating cross-contamination of products and reducing general housekeeping costs |
![]() |
Health & Safety: No need for tools to remove or install the connector in difficult positions, ensuring a much safer environment for staff. |
![]() |
Explosion resistant: The removal of dust and the antistatic properties of the BFM® Fitting products reduces the risk of secondary explosion. |
![]() |
Reduced downtime: Fast and efficient cleaning in between product runs means downtime is significantly reduced. |
![]() |
Easy installation: The simple snap-fit of the BFM® connector makes change-overs easy, and standard BFM® Connectors fit correctly. |
Dairy Hygiene Improved with BFM fittings
A leading New Zealand dairy plant had a major challenge with hygiene in their blending filler room.
A vibratory discharging cone was connected to the hopper via a traditional connecting sock and steel clamps. There was excessive dust leakage and product build-up in the joins – a major hygiene issue.
Since installing the BFM® fitting system, the filling room operators are ecstatic about how their work environment is now dust-free and a “pleasure to work in”.
They no longer spend hours cleaning powder off the surfaces in the filling room or have to regularly remove the messy wire-clamps and socks from the machinery to remove the product build-up between the connectors.
